


PHOTOVOLTAICS
„Capture of production- and process data in real time, based on industry 4.0 for higher productivity and significant cost reduction“
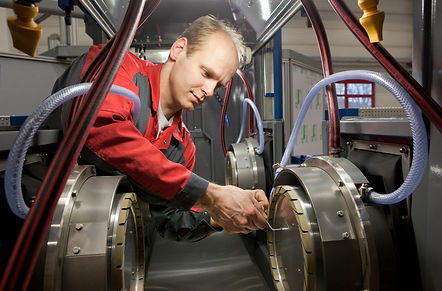
Our core competence in photovoltaics and semiconductor poly-Si processing is the mechanic cutting, notch.-and roundgrinding, surface.- and chamfergrinding, squaring, rod.-and profilgrinding / polishing of silicon ingots.
Arnold can offer innovative, stand alone machines, as well as machines developed according to your individual requirements and specifications, such as complete processing centres and custom-tailored complete systems with an automatic linkage of all production processes and an intelligent assembly control system.


GRINDING
Precision grinding machines for poly-, mono and multicrystalline silicon.
We built our first Silicon grinding machine in 1995. Due to the continuous development in the area of construction, processing, control engineering and handling, our machines now belong to the most efficient high-end grinding machines worldwide.

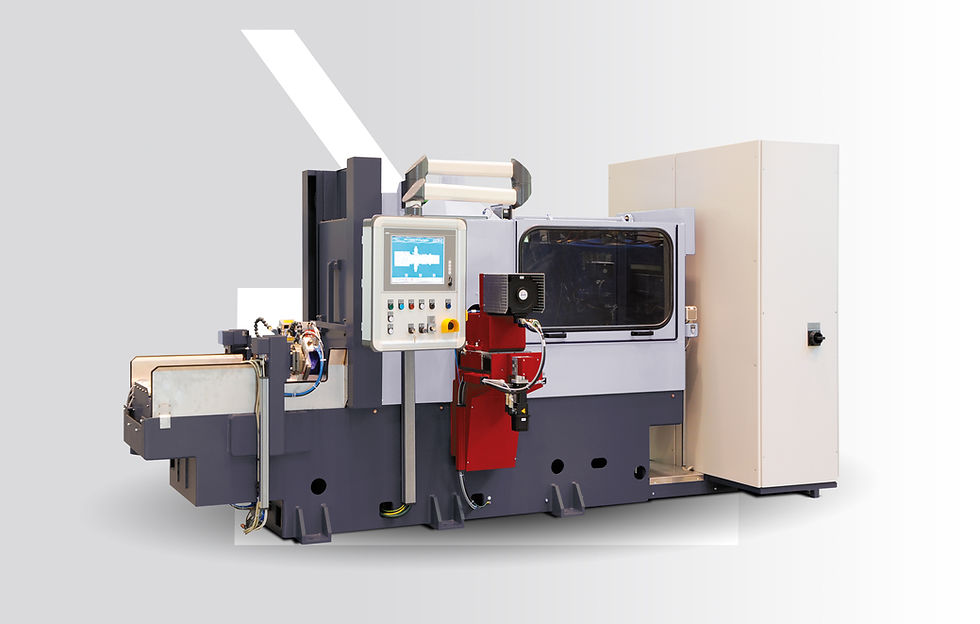
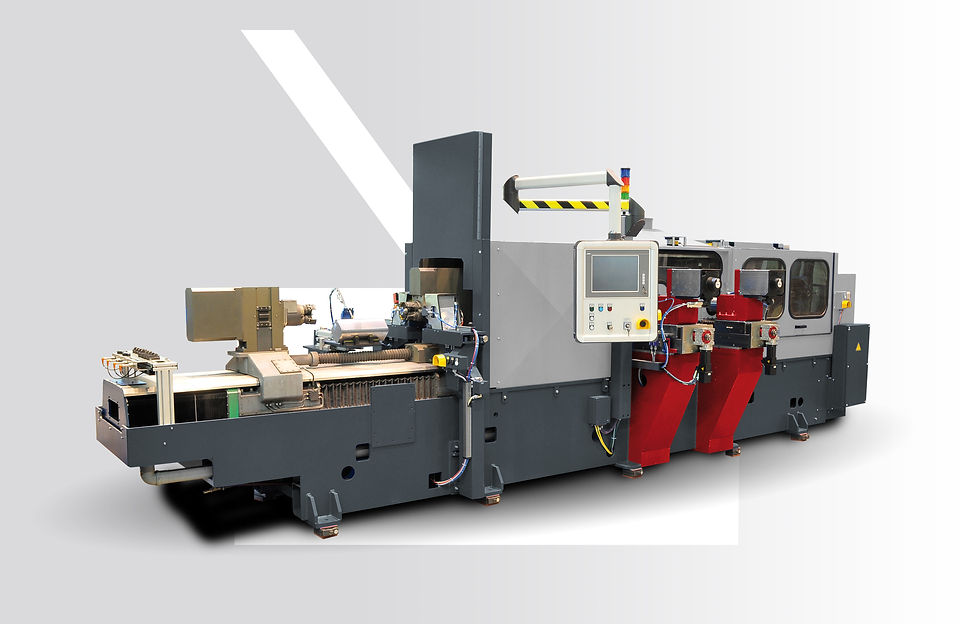




CUTTING
Arnold cutting machines

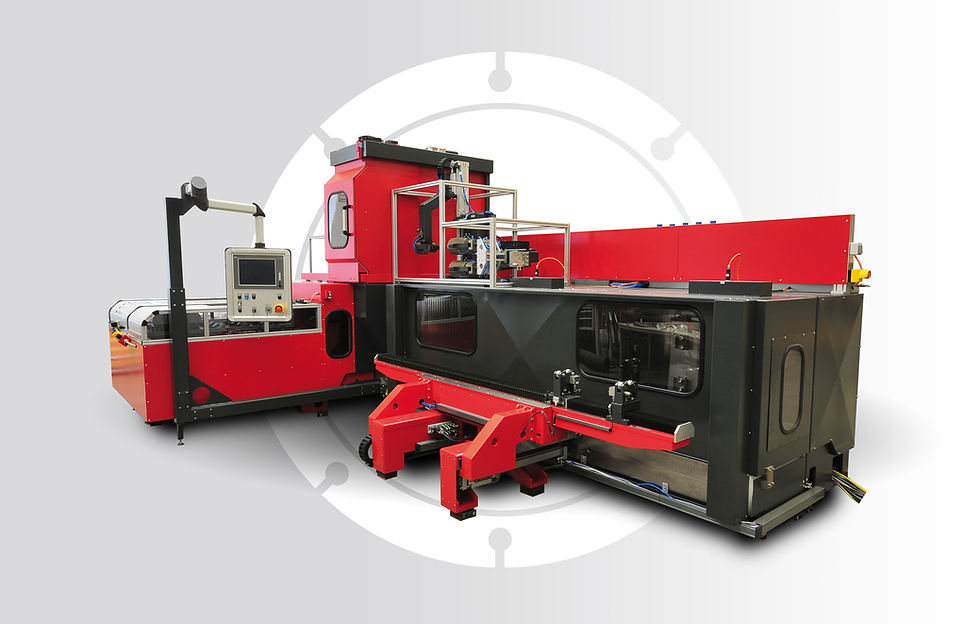
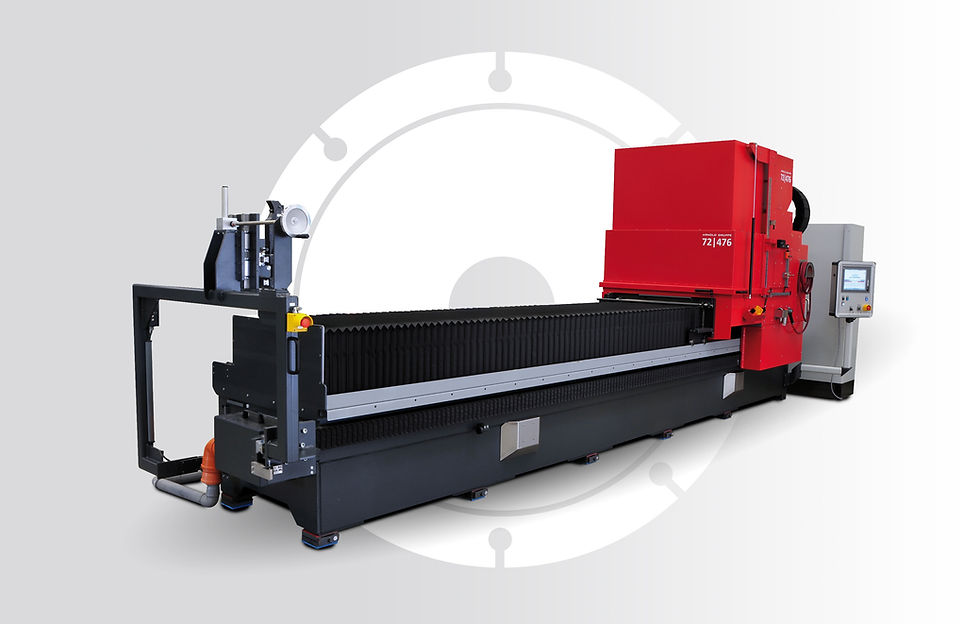




AUTOMATION
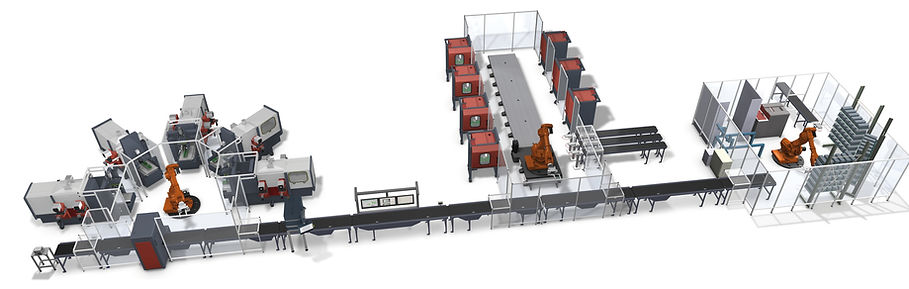
Grid Parity through Automation
Efficient wafer production already starts within the brick manufacturing process. Automated manufacturing processes are the basis for reproducible production quality, a high production volume as well as reduction of material losses and is as consequence the main driver to reduce production costs.
ARNOLD is the leading manufacturer of automated production systems for processing mono and multi crystalline silicon bricks. Flexible and intelligent manufacturing centres for fully automated brick production are counted among the core competences.
ARNOLD offers a modular system concept of process machines and manufacturing automation – everything from one source:
■ grinding and cutting machines with fully automated manufacturing processes and outstanding process stability
■ robot-based handling systems for automatic loading and unloading of the process machines
■ robotic brick glueing systems including fully automated assembly of silicon bricks on wire saw beams
■ conveyor systems for automated brick transportation to the individual machine centres
■ 100% quality monitoring of all bricks produced for continuous recording of brick geometry, SiC-inclusions as well as carrier-lifetime
■ intelligent process supervisory control for a precise acquisition and analysis of production and quality related data.




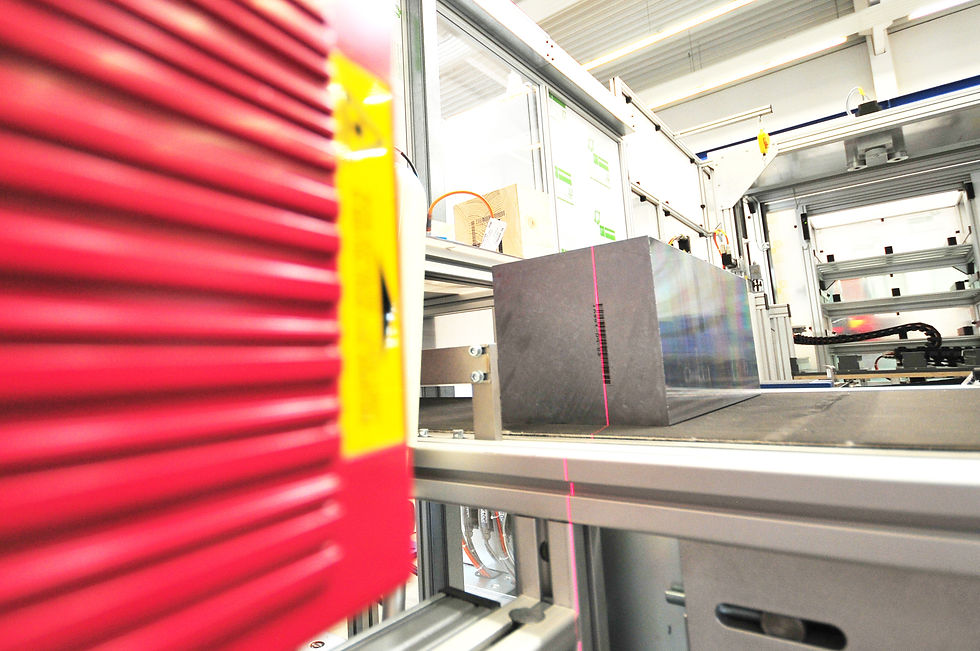

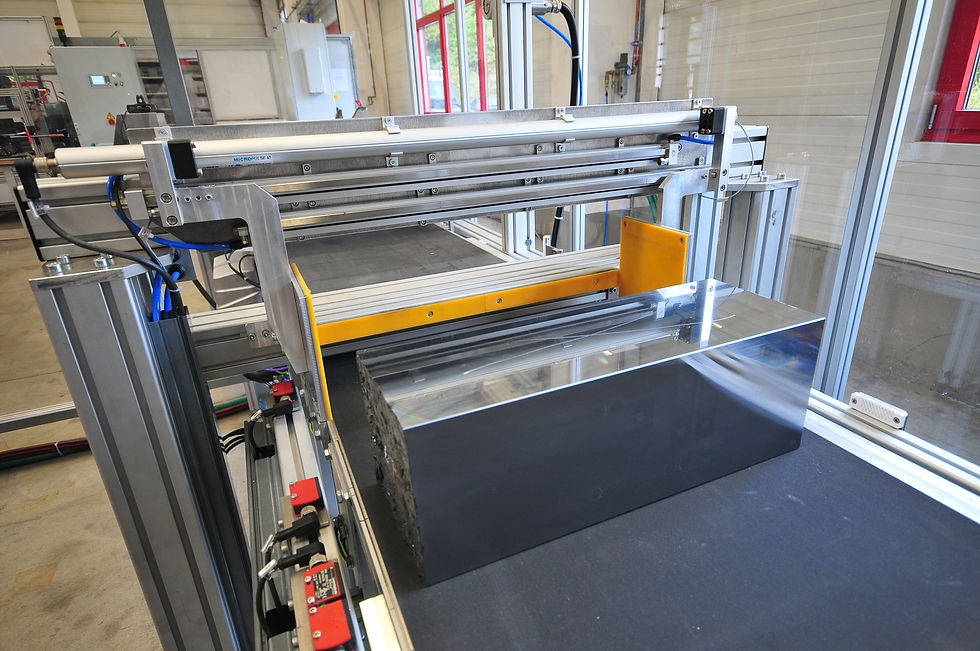

ARPAT - CLOSED-LOOP PROCESS DEVELOPMENT

ARPAT provides transparency and efficiency in the silicon brick production
The unique ARNOLD-Remote-Produktion-Analysis-Tool „ARPAT“ for transparent production processes and for a constant improvement of production quality and cost efficiency - achievable by the so-called „Closed Loop Process-Optimization”.
Data recording is starting again with the modified production and process recipes. Thus closing the loop of continuous process optimization. This systematic approach constitutes a significant improvement of overall cost efficiency.


Advantages and benefits of data collection
ARPAT Advantages
100% cost transparency
100% process transparency
100% quality transparency
ARPAT benefits
Continuous process optimization
Continuous increase in quality
Reduction of lead time
Reduction of material consumption
Profit increase

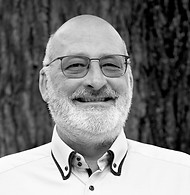